最新の事例
FUSE
株式会社丸善 様
生産計画の見える化や不良の追跡が可能になり、現場の作業効率向上に繋げられた
多品種小ロット製品の仕事の依頼が増えている中で、紙やExcelを使った運用のままでは、回し切れない可能性があったが、システムを導入することで現場作業や事務作業の作業効率がアップした。
導入前の課題
- 依頼が増えている多品種小ロット製品の生産体制を整える必要がある
- 現場の状況なども含めて複数拠点の情報を管理していきたい
導入サービス
生産管理システム FUSE(フューズ)
受注管理/作業管理/出荷管理/EDI取込/図面管理/仕入・外注管理/進捗管理/工程管理/生産計画/作業実績集計/在庫管理/ピッキング管理/製品構成管理/作業動画管理/不良管理/売掛管理/買掛管理
導入による効果
- 全体の生産計画が見える化でき、作業者が自分の判断で主体的に作業を進められるようになった。
- 各種事務書類作成の時間の削減とヒューマンエラーの低減につながった。
- 不具合のトレースがより便利になった。
- 1週間程度の時間を要していたISOの審査の資料準備が、関連する資料をすぐに画面に表示できるようになったため、探す手間が軽減された。
Freely
神戸化成株式会社 様
複数拠点間や部署間での生産計画をホワイトボードを使用して立案・運用していたため、計画の共有がスムーズにできておらず、計画変更の度にホワイトボードの内容を書き直していたため記載漏れや転記ミスなども発生していたが、生産計画のWeb化によりリアルタイムで複数メンバーへの情報共有が可能になり、記載漏れや転記ミスなどの人的ミスも解消!
導入前の課題
- 生産計画をホワイトボードで行なっていたため、拠点間や部署間で計画の共有がスムーズにできていなかった
- 計画に変更がある毎にホワイトボードの内容を書き直していたため、ホワイトボードへの記載漏れや転記ミスも発生していた
導入サービス
生産スケジューラFreely(フリーリー)
導入による効果
- 生産計画のWeb化によりどこからでも複数メンバーで瞬時に情報把握
- 計画変更も簡単でリアルタイムに共有
- 記載漏れや転記ミスなどの人的ミスも解消
事例紹介
FUSE
有限会社本間製作所 様
現場作業者ごとの生産性の見える化に成功し、個人評価の反映にも繋げられた
工程管理ができておらず、作業進捗が見えないため納期遅れが常習化していたが、システムを統合できたことで現場の作業員が製造業務に集中できるようになったため、現場の作業効率アップした。
導入前の課題
- 工程管理ができておらず、作業進捗が見えないため納期遅れが常習化している
- 図面を探し出すのが手間で煩わしい
導入による効果
- システムから各種事務書類を出力できるようになり、書類作成の労力や誤記などの間違いを削減!
- システムを統合できたことで現場の作業員が製造業務に集中できるようになったため、現場の作業効率アップ!
- 現場作業者ごとの生産性の見える化に成功!個人評価の反映にも繋げられた
Freely
株式会社 神戸製鋼所
加古川製鉄所 製銑部 資源循環室様
“ホワイトボード上での消して書いてのムダな時間を年間2,000分以上削減
加古川製鉄所で製造した製品のほとんどは船舶によって出荷されており、製銑部 資源循環室では「いつ」「どの出荷岸壁(バース)で」船積み出荷するかホワイトボードで会議を行って計画立案、調整をしていたが、システム上で情報を管理することによって会議前後の無駄な時間を年間2,000分以上削減!
導入前の課題
- 計画立案調整会議をホワイトボードを利用して実施しており、情報の転記作業としてのムダや転記の抜け漏れが発生していた
- 会議中の変更内容をホワイトボード上で加筆・変更していたため、その都度中断を余儀なくされていた
導入サービス
生産スケジューラFreely(フリーリー)
導入による効果
- ファイル取込/出力機能により、転記作業時間削減!所要時間が45分→0分に!
- 転記作業による人的ミス(抜け漏れ)も解消!
- ドラッグ&ドロップの簡単操作でスムーズに会議進行が可能!
- クラウドサービスなのでテレワークでも会議を実施可能!
その他の事例
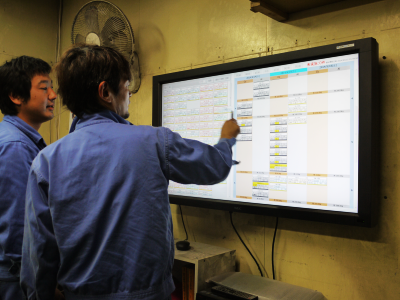
作業進捗の見える化で
納期遅れを削減!
工程管理ができておらず、作業進捗が見えないため納期遅れが常習化していたが、大型タッチパネルを活用した進捗共有で納期遅れが1/3に減少
導入前の課題
- 工程管理ができておらず、作業進捗が見えないため納期遅れが常習化している。
- 社員のITスキルが低く、複雑なシステムは使いこなせない。
- 鋳造の専門技術が暗黙知となっており、技術継承がうまくいかない。
導入による効果
- 大型タッチパネルを活用した進捗共有で納期遅れが1/3に減少。
- 砂塵の多い鋳造工場内で、防塵カバー付きのタブレットを利用した実績入力を実現。
- 高齢の社員でも、タブレットで現場から実績登録が行えるようになり、リアルタイムの進捗把握が可能になった。
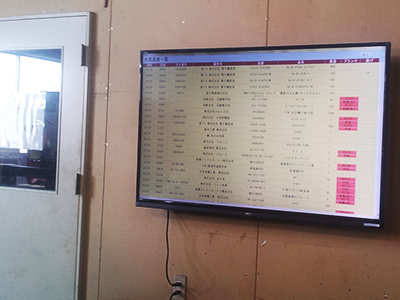
工場の見える化で
特急対応を削減!
作業遅延や着手漏れの発見が遅れ、納期直前の特急対応が度々発生していたが、現場への指示と進捗状況を大型モニタに常時表示することで、作業遅延や作業漏れの防止、円滑な個別フォローが行え、特急対応が減少した。
導入前の課題
- 工程管理ができていないため、作業指示書の納期を基に各作業者の判断で作業に着手しており、作業遅延や着手漏れの発見が遅れ、納期直前の特急対応が度々発生する。
- 作業の進捗確認は、経営者が工場を駆け回って直接確認しており、負担が大きい。
- 顧客から納期問合せの電話を受けた際、進捗が見えないため即答できない。
導入による効果
- 工場内に大型モニタを設置し、現場への指示と進捗状況を常時表示。これにより、作業進捗を作業者全員が把握することが可能となり、作業遅延や作業漏れの防止、円滑な個別フォローが行え、特急対応が減少した。
- 経営者も個別の進捗確認を行う必要がなくなり、管理時間が1/4に減少。
- 顧客の問合せにも即座に対応できるようになり、顧客満足度が向上した。
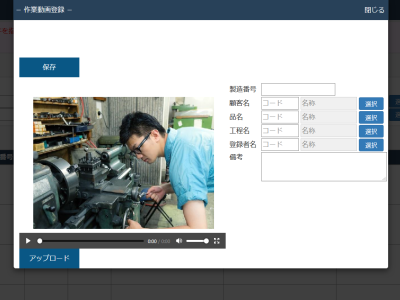
作業ノウハウ蓄積による
技能伝承!
技術ノウハウを各作業者ごとに独自のルールで管理しているため、共有、および活用がうまくいっていなかったが、作業指示書に紐づけて登録管理できるようになったため、 誰でも簡単に必要情報を参照できるようになった。
導入前の課題
- 熟練者の技術ノウハウが暗黙知となっており、技術継承がうまくいかない。
- 作業動画や加工時のメモ情報を各作業者ごとに独自のルールで管理しているため、技術ノウハウの共有、および活用がうまくいかない。
導入による効果
- 作業指示書に紐づけて作業動画などの技術ノウハウを登録管理できるようになったため、誰でも簡単に必要情報を参照できるようになった。
- また、試作品や類似製品を製造する際にも、材質や形状などで検索することで、技術ノウハウを活用できるようになった。
- 熟練者の技術ノウハウは、研修教材としても活用できるため、技能伝承や若手育成に寄与している。
生産現場のお悩み・課題を相談したい
中小製造業様への専用システム開発で培ってきたノウハウをもとに、専門スタッフがご相談を承ります。
ご不明な点は気軽にお問い合わせください